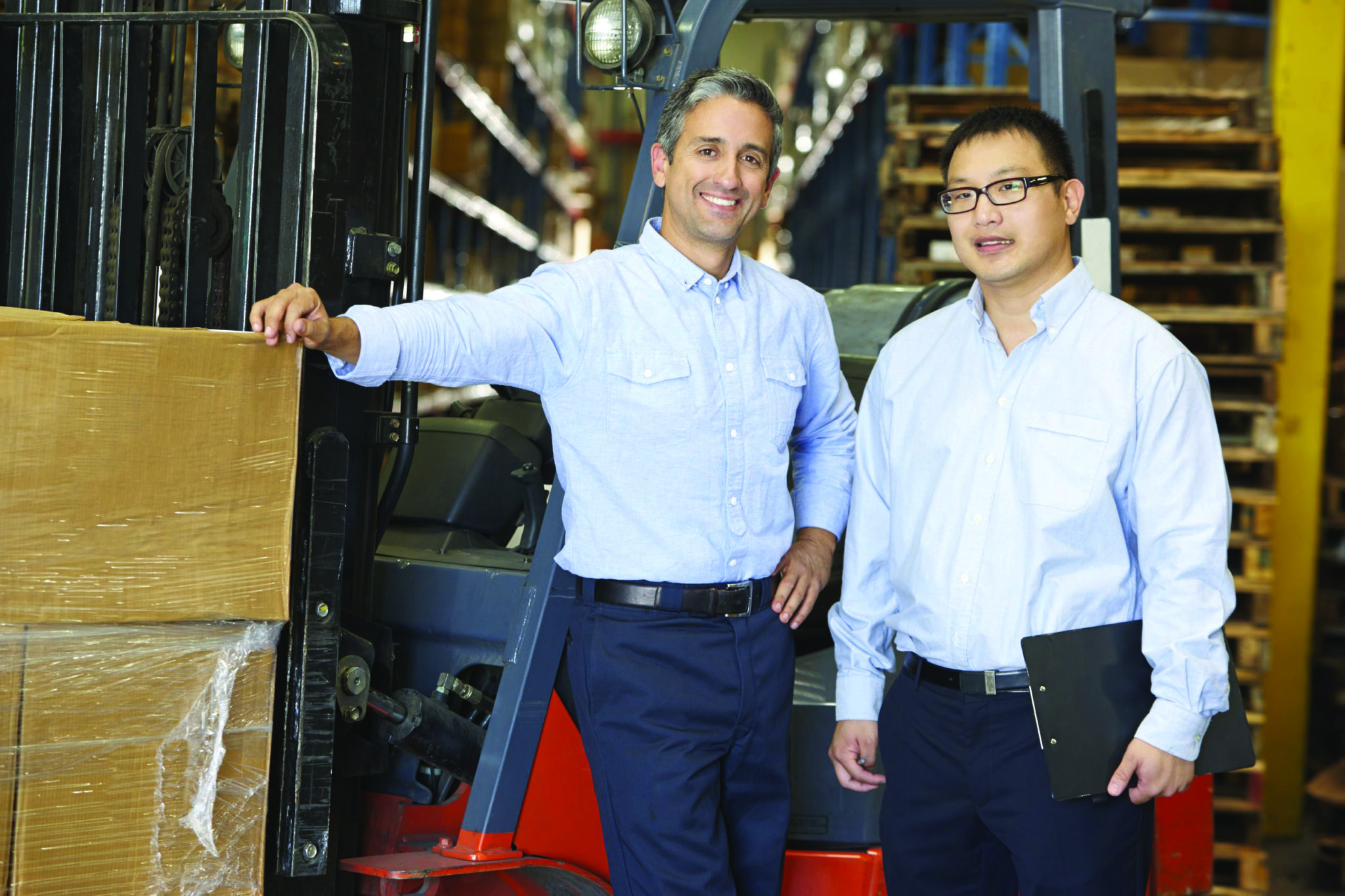
Tackle The Complexities Of SAP Inventory Management Step-By-Step. We’ll Show You How.
You can master SAP inventory management.
SAP inventory management is no easy task. With so many moving pieces, it’s difficult to keep tabs on every key metric of your plant’s performance. Luckily, using SAP inventory software gives you plenty of tools to simplify inventory management. These tools can help you identify what’s working and what needs attention. Most importantly, they can help you move product through with as little wasted time and wasted money as possible–and they can help you optimize for SAP eCommerce, which is fast becoming the norm in B2B.
Inventory management is a broad topic. We’ll break this article into definitions and best practices, with several chapters in each section. But first—why inventory management?
The strategic goal of SAP inventory management
Organizational efficiency is the goal of inventory management. You want to eliminate waste in process, product, and work hours. When you eliminate waste in each of these categories, that translates into a better bottom line. But determining where the balance falls can be challenging. How do you stock enough inventory to meet demand, while not storing so much that the cost of maintaining inventory cuts into your targeted margins? It’s important to note that process efficiency doesn’t only apply to distribution centers that sell to your customers through phone, fax, email, or a SAP customer portal solutin. An internal distribution center can also drive up organizational costs through inefficient processes. Whether you’re managing inventory internally, or in a customer-bound scenario, you need to leverage intelligent inventory management strategies for better efficiency and lower cost. That way, you get the most out of your SAP inventory management systems. Now let’s move on to components that make up SAP inventory management. We’ve organized the information around 12 questions.
Table of Contents
1. What is SAP inventory management? 2. How does SAP e-commerce change inventory management practices? 3. What types of physical locations does SAP provide for inventory assignment? 4. What are movement types in SAP? 5. What are SAP inventory management T-Codes? 6. What is Material Management in SAP? 7. What is SAP WMS? 8. What is a material document in SAP? 9. What is a physical inventory in SAP? 10. What is the SAP PP module? 11. What is the SAP QM module? 12. What is meant by SAP SD?
1. What is SAP inventory management?
First off, a definition: inventory management is the practice of controlling inventory flow for maximum organizational efficiency. But what does that mean in practice? We can break inventory management into several discrete processes:
- Monitoring data—Gaining knowledge of inventory levels and change in levels over time
- Interpreting data—Generating action items based on the data
- Executing action items—Assigning the action items to your team
If you work in inventory management, it’s best to keep each of these processes separate. Even if you’re responsible for all 3 of them, the best practice is to perform one process at a time. Gather all your data first; then stop gathering data and work on an interpretation; then go out and execute your action plan.
Of course, keeping these processes separate is even easier if you’re managing a team. In that case, however, you should make some effort to communicate where each process falls in the overall inventory management strategy. For example, if you assign action items to a team member, you should communicate to him or her how you came up with the action item and why it’s important.
2. How does SAP e-commerce change inventory management practices?
The answer to this question depends on how your SAP B2B e-commerce solution is set up. If you have a powerful, real-time integration between Magento and SAP, your inventory data following best practices will appear live in your e-commerce store. Your management process won’t need to account for “inventory lag,” because the moment a material is purchased via e-commerce, your e-commerce store will update the inventory quantity in SAP. You will be able to run Available-to- Promise (ATP) checks real-time on the web.
However, if your e-commerce solution relies on batch updates to maintain inventory data, your inventory management process will have to take that into account. If the day’s e-commerce orders aren’t posted to SAP until a nightly batch update happens, then it’s possible that a phone order earlier in the day will claim the last stock of a material, leading to an unexpected backorder when e-commerce orders are posted.
At scale, this can be a costly problem, and your inventory management projections will need to take this into account if you’re relying on batch updates between e-commerce and SAP. That’s why we recommend real-time integration via web services for SAP e-commerce using the Corevist Platform.
3. What types of physical locations does SAP provide for inventory assignment?
There are two organizational levels that have to be created in SAP for each inventory center. They are:
- The plant—This is the high-level physical location to which materials are assigned.
- The storage location—This is a specific area within the plant where product is stored.
Each location must be created in SAP so that inventory can be assigned appropriately. You can use these locations to track where inventory is in the supply chain process—both whether it has arrived at your plant, and where it’s actually stored in the plant.
4. What are movement types in SAP?
SAP includes a feature called “goods movement” that allows you to track when and how goods change hands. These movements can indicate handing off goods within your organization as well as a handoff to a customer or vendor. They are important indicators of where a material is in the supply chain process.
Goods movements fall into several high-level categories. Each of these categories contains many goods movements, each of which is controlled with its own unique 3-digit code. Note that each movement will generate a material document (see below).
- Goods receipt—The material is coming in from a supplier or moving within the organization. You can place the goods in a hold for quality inspection, or release them for their next movement.
- Goods issue—The material is assigned to a production process, or sold to a customer. Both actions reduce the inventory level at the plant and assign the goods to a production order or sales order respectively.
- Return delivery—The material is being returned from a customer or vendor.
- Transfer posting—The material is moving from one place to another within the organizational plants while financially staying on the books.
For a full listing of all the 3-digit goods movement codes and how they’re used, see the SAP Wiki – Movement types.
5. What are SAP inventory management T-Codes?
T-codes, or transaction codes, control the movement of materials into, through, and out of your SAP system. Each t-code has its own unique 4-digit name, which is a combination of letters and/or numbers.
Important t-codes include:
- MIGO – Goods movement
- MB1A – Goods withdrawal
- MB1C – Goods receipt
- MBST – Cancel material document
- MB02 – Change material document
There are many, many t-codes related to inventory management. For a full list of inventory management t-codes within the Material Management module, see this page at TCodeSearch.com.
6. What is Material Management in SAP?
The Material Management module in SAP handles the organization’s procurement processes. It also handles all the inventory processes in SAP. The Warehouse Management module was originally part of Material Management, but it has since been spun off as part of the Logistics Execution module.
While the Material Management module covers more than just inventory management, it is an essential part of the inventory management process in SAP. It ensures that your organization handles input and output of product as efficiently as possible.
For more information, see SAP MM Overview at Tutorials Point.
7. What is SAP WMS?
The SAP WMS (Warehouse Management system) enables you to manage all aspects of warehouse logistics in your organization, regardless of the level of complexity, through various automations. The module offers high-level control, such as monitoring the movement of product, as well as visibility into details like assignment of specific storage locations and storage bins. It enables you to model your warehouses and DC (distribution centers) in a three-dimensional fashion (bin-rack-row).
SAP WMS also controls all goods movements within the warehouse. This complex, unending task is greatly simplified when you use barcode scanners to input the data—a method which the module supports.
For more information, see SAP WM Module at ERP Great.
8. What is a material document in SAP?
A material document is generated whenever a goods movement is posted. The document serves as the official record of the movement and is a key component of the Inventory Management system. If there is no document to support a movement, it is believed not to have occurred.
Material documents follow a standard structure. They contain a header, and at least one item. They run as long as required, with each item describing only one movement.
For more information, see The Document Concept in SAP Documentation.
9. What is a physical inventory in SAP?
Physical inventory refers to the inventory quantities that are actually present in the warehouse. These numbers may not match what SAP shows. If that’s the case, you need to determine why the discrepancy has occurred and then rectify it. Note that companies are required by law to report inventory levels accurately.
Inaccurate inventory levels in SAP send shockwaves throughout your organization’s supply chain. If SAP reports a different stock level than what’s actually available, your Sales Department may commit to a sale that isn’t physically possible—or they may be unaware of product that can actually be sold.
But Sales isn’t the only process affected by inaccurate inventory. This problem harms internal processes, too. If inventory levels are actually lower than reported, a downstream production process will hit a snag when it turns out that the raw materials aren’t available.
Inaccurate inventory also skews management’s view of the financial situation of the organization. If SAP displays less stock than is actually in the warehouse, management isn’t aware of stock that is costing the organization money by sitting and doing nothing. Likewise, if SAP is showing more stock than the warehouse actually has, management isn’t aware of reordering that needs to occur.
10. What is the SAP PP module?
The SAP Production Planning (PP) module handles everything related to material requirements planning (MRP). It allows managers to structure manufacturing processes so that they meet demand efficiently and without surprises. The module controls raw materials required for production processes, automated material requisitioning, planning resources required to hit target capacities in production, and more. It is fully integrated with the other modules that are relevant to inventory management (QM, SD, MM, FICO).
The BOM (bill of material) is an important document in PP. It allows you to define all of the components required to complete a production process and specify the quantity of each component required.
For more information, see Introduction to SAP PP at Guru99.
11. What is the SAP QM module?
The SAP Quality Management (QM) module controls the quality of products. It allows you to define how quality is measured, record measurements, and determine what action to take to meet your quality requirements. It is an essential part of processes like procurement, production, sales, and more. The module is fully integrated with other modules that are relevant to inventory management (MM, PP, PM).
There are four components of the module that you can leverage to conduct quality assurance and develop relevant action items. They correspond to the four stages of a healthy quality assurance process:
- Planning inspections
- Quality notifications
- Quality inspection
- Quality reports
For more information, see this article at The Balance.
12. What is meant by SAP SD?
The SAP SD (Sales and Distribution) module controls sales orders and the distribution of those orders. It handles every part of the process, including pre-sales quotes, sales order creation and processing, shipping and relevant document creation, billing and relevant document creation.
SAP SD integrates fully to other modules in SAP, including FI, CO, MM, and PP. It is the final module that product passes through on its way to the customer. It allows you to track all types of sales data and use it to for planning purposes in inventory management.
For more information, see this article on ERP SD on the SAP Wiki.